Even before the establishment of the State of Israel, faculty, students, and alumni of the Technion helped develop and manage water resources in a desert land. They contributed to the national water carrier that brought water from the Kinneret (Sea of Galilee) in the north to the drylands in the south. They improved technologies for water treatment, desalination, and drip irrigation. These efforts have turned Israel from a water-deficient to a water-abundant country.
Today, Israel leads the world in water reclamation, recycling more than 90% of its wastewater for use in agriculture and industry. No longer reliant on the Kinneret, Israel’s five desalination plants provide the bulk of the country’s drinking water. Complex systems carry diverse water types from diverse water sources for diverse water needs.
But far from resting on its laurels, improving the sustainability and quality of water and water management facilities remains a major priority for Israel and for the Technion. The University established the Stephen and Nancy Grand Water Research Institute (GWRI) in 1993 to address these challenges through science, technology, engineering, and policy development.
The GWRI comprises more than 40 researchers from various faculties, including civil, environmental, mechanical, and chemical engineering, as well as chemistry, biotechnology, and more. They publish about 200 papers a year on topics from water resource management to aquaculture systems to feed a burgeoning world population. While its focus is on the needs of Israel, it is also very much involved internationally.
“One-third of the world’s population lives under water scarcity conditions,” said Professor Eran Friedler, director of the GWRI and the Henry Goldberg Academic Chair in the Faculty of Civil and Environmental Engineering. He is also a Technion alumnus, having received a Ph.D. in environmental engineering in 1994.
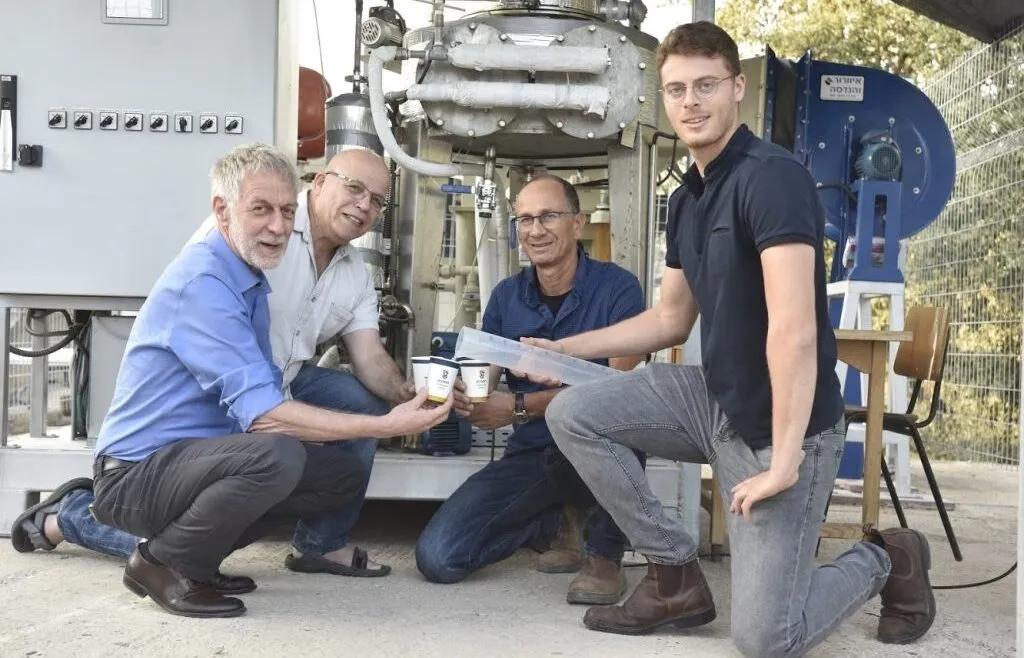
“The number will only increase due to population growth, urbanization, and climate change. And this can lead to political instability and refugees,” Prof. Friedler added.
And that’s the reason he co-invented a system that produces clean water from the air with a colleague, Professor David Broday. Their atmospheric water generator harvests air moisture by an innovative continuous liquid desiccant system. Energy is only invested when condensing the vapor into liquid water. It even works in desert regions and can run on solar energy. They founded a startup, H2OLL, to commercialize the product.
Prof. Friedler’s area of expertise in developing alternative water resources and improving delivery systems extends to research on wastewater reuse and methodologies to harvest rainwater. He is looking into ways to store rainwater in tanks that can be released when the water flow in drainage pipes is low. This rainwater can be used in toilets, washing machines, and dishwashers. And with some treatment, it could be used for drinking water.
“With climate change, rain events are going to be more severe. If we can store the water through harvesting, we can reduce the amount of drainage water in cities while supplying water to various uses.”
Other GWRI researchers are working on ways to reduce the environmental impact in water treatment and desalination. Some are working on organic methods to remove pollutants.
“Even at the end of the traditional treatment process, there are still pollutants in very small concentrations that are not removed,” said Professor Yael Dubowski. “Residues of pharmaceuticals, pesticides, personal care products — we don’t know enough about the problems they could cause when water containing them is used for agriculture.”

Prof. Dubowski has investigated a chemical-free advanced oxidation process that is based solely on ultraviolet light. Such radiation breaks the water molecules and generates the radicals needed for pollutants’ oxidation. It holds promise for an additional step in the water treatment process.
Associate Professor Adi Radian is studying the natural, positive processes that occur in the environment to breakdown pollutants. She wants to mimic them to improve remediation in engineered systems.
“Clay minerals are plentiful, cheap, natural, nontoxic, and have huge surface areas,” she explained. “Clay is often used to soak up spills and bad smells — think cat litter.” Prof. Radian is working on changing the chemistry of clay to make it adsorb (bring to the surface) rather than absorb pollutants. Depending on the properties of the pollutant, she can change the properties of the clay.
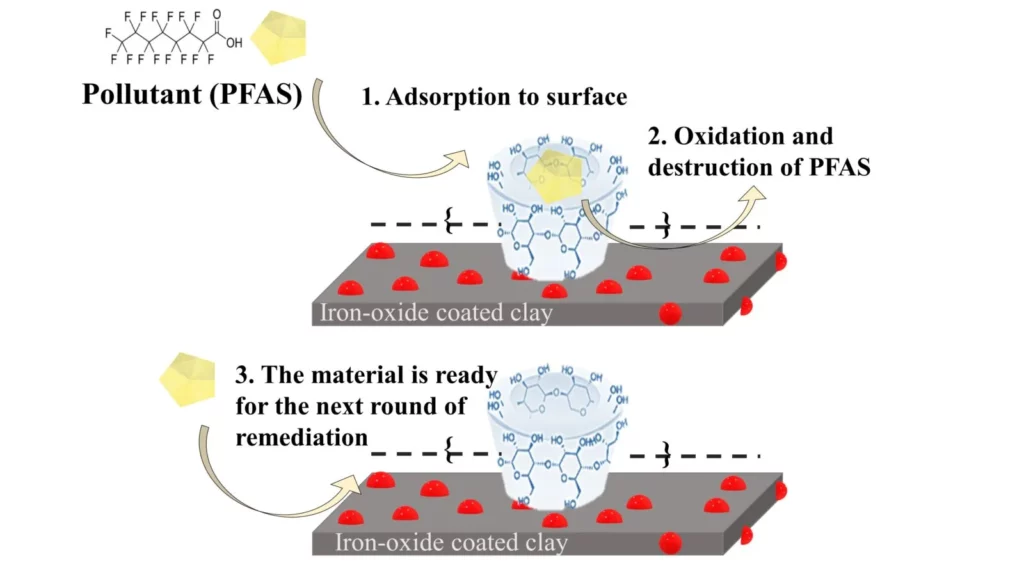
She has already had great success with removing “forever chemicals” from water systems. These are toxic substances like Teflon and other nonstick materials that repel water. Using iron oxide coated-clay together with cyclodextrin polymers, she was able to remove 90% of them from contaminated water in just minutes.
Since Israel has been using desalinated water for drinking and reclaimed wastewater for agriculture in greater quantities and longer than any other country, Profs. Friedler, Dubowski, and Radian, and other Technion researchers are sure to play a major role in solving the world’s water scarcity problems. They acknowledge that the key is finding environmentally sustainable and affordable means to do it.